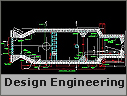 | Design Engineering |
An essential basis for refractory engineering is process knowledge. Only when one knows and understands as to why something happens, is it possible for them to make modifications/optimization to the existing systems. An optimized refractory lining is fundamental to enhanced operations. Along with the appropriate materials, the correct engineering is essential. To prolong refractory life in a sustainable manner, an individual vessel has to be regarded as a whole and comprehensive examination is required.
|
|
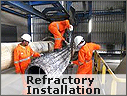 | Refractory Installation |
Along with the usage of the appropriate refractory, it has to be installed in a designated manner to achieve optimum performance. Projects lacking the necessary infrastructure and expertise for refractory installation could outsource it to the specialists which include processes like demolition of existing linings, surface preparation, anchor system wielding, pneumatic 'gunited' linings, vibration cast linings, rammed linings, fireproofing, pre-fabricated shapes, ceramic fiber linings, shop and field installation, undertaking comprehensive QA/QC program etc.
|
|
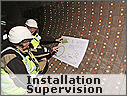 | Installation Supervision |
During the installation of refractory, it is essential to adhere to the correct methods of application to ensure optimum refractory life. Having a specialist to supervise, cross check and implement best practices will help to achieve the desired results. This will also help in identifying equipment challenges and weak spots, which can be managed by the supervisor by using special installation techniques/products. The supervisor can also identify the modifications needed for the equipment which can help in improving overall refractory life.
|
|
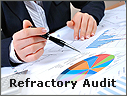 | Refractory Audit |
Refractories are a critical part of the operation of most high temperature industrial processes in industries such as Cement, Steel, Lime, Aluminum etc. They are frequently a major cost item, both in general maintenance and also the unscheduled downtime of production units arising from premature refractory failure. Refractory technology is changing rapidly and the price of refractory materials is continuing to escalate. All users must conduct regular audits of their refractory purchases.
|
|
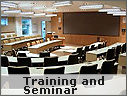 | Training and Seminar |
Training and seminar sessions add great value in understanding the relationship between refractories and processes. It keeps the personnel updated on new materials, processes and best practices of their industry. It is widely accepted that regular training and seminars help achieve better refractory performance resulting in optimum production.
|
|
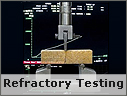 | Refractory Testing |
Special testing methods have been established to provide assurance that the refractory purchased are capable of meeting the process requirements. Refractoriness under Load (RUL) and Creep in Compression (CIC) identify the deformation resistance of a test piece under a defined load and temperature/time factors. The modulus of rupture at high temperatures (HMOR) is determined with a hot modulus of rupture tester. The melting behavior of these refractories is determined indirectly through comparison with so-called 'Seger' cones (PCE - Pyrometric Cone Equivalent).
|
|
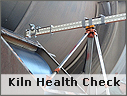 | Kiln Health Check |
Analysis of kiln alignment and shell ovality characteristics are important tools which can help to improve or maintain the mechanical stability of the kiln. Due to the difference in kiln shell outer and inner diameter, the outer revolution is more than the inner revolution. The slippage of the shell inside the kiln is called migration. Migration is an important tool to measure air gaps, which are essential for shell expansion.
|
|